To consider an application for financing, fill out the form and send it to us by e-mail along with the project brief, or contact our experts
According to some reports, 50% of hydroelectric power plants in Africa are operated with obsolete turbines, which have long exceeded 35 years.
The benefits of hydropower, in particular the potential of running water, have been exploited since ancient times.
Hydroelectric power is considered to be the most reliable and cost-effective technology compared to other renewable energy sources.
Hydroelectric power plants are environmentally friendly; they are stable and safe sources of electricity. Modern hydraulic units are very efficient in terms of operating costs, which are relatively low due to the high degree of automation.
HPPs use energy production technologies with high efficiency and flexibility, which are extremely important for maintaining the balance of the power system.
However, technology is becoming obsolete, and today many power generating companies are faced with the need for inexpensive but important improvements.
Some of the oldest hydropower plants with an installed capacity of 2 GW or more:
Name | Years of construction | Inst. Capacity, GW | Country |
Hoover Dam | 1936-1993 | 2,1 | USA |
Grand Coulee | 1942-1991 | 6,8 | USA |
Zhigulyovskaya | 1955-1957 | 2,5 | Russia |
Volga GES | 1958-1961 | 2,7 | Russia |
Chief Joseph Dam | 1958, 1979 | 2,6 | USA |
Niagara Falls | 1961 | 2,6 | USA |
Macagua | 1961, 1996 | 3,2 | Venezuela |
Bratsk GES | 1961, 1966 | 4,5 | Russia |
Cleuson-Dixence | 1965, 1998 | 2,1 | Switzerland |
Aswan | 1967, 1970 | 2,1 | Egypt |
In many cases, upgrading old hydropower plants is much more profitable than building new ones.
Costs, environmental impacts, social impacts and timing may be more appropriate in this case.
The main goal of modernization and repair work is to extend the life and improve the performance of the machines, thereby increasing the availability and reducing the operating costs of the HPP. In some cases, the goal of modernization is to increase capacity and energy production. This can be done by replacing the old electromechanical equipment with a new one with higher technical parameters.
In addition to improving safety and energy efficiency, the use of standard designs of hydropower equipment is considered to be the determining trend in the modernization of hydropower plants.
It is also desirable to use standardized parts in the engineering design of equipment, which helps to reduce the cost of projects and facilitate the maintenance of the plant. Among the latest requirements, experts highlight the use of automatic control systems to ensure stable operation even with large fluctuations in water speed and pressure.
Our team is ready to offer financing and start implementing your project anywhere in the world.
To find out more, contact our specialists and request a consultation.
Recent trends in the modernization of hydroelectric power plants
Together with partners, we also use the best practices of other industries to make hydropower plants reliable and efficient.
In the coming years, hydropower will see significant improvements, especially in terms of facility size, hydraulic efficiency and environmental protection.
Improvement of hydraulic turbines
Over the past decades, the efficiency of hydraulic turbines has gradually increased, and now the energy conversion efficiency of modern hydroelectric power plants exceeds 95%.These values can be achieved through extensive modernization of many existing turbines. Computational fluid dynamics (CFD) has greatly simplified the detailed study of fluid flow characteristics and optimization of the turbine impeller design.
Continuous improvement of hydraulic turbines pursues the following goals:
• Increase in power rating and improve efficiency.
• Achieve high flexibility of work in accordance with market needs.
• Increased availability and reduced maintenance costs (reduced need for repairs due to damage, cavitation and abrasion).
• Improving environmental performance (increasing fish survival, efficient use of river flow and maintaining water quality).
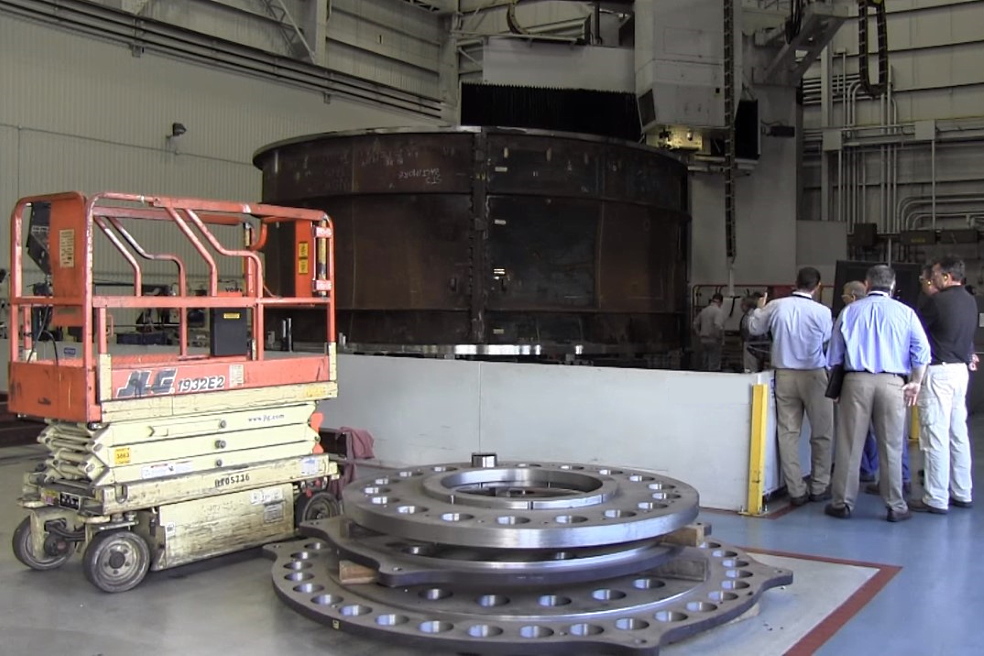
Some innovations are aimed at limiting the impact of HPPs on the environment.
For example, aeration systems use low pressure water to pass through turbines to provide additional airflow. This increases the concentration of dissolved oxygen in the aquatic environment.
To eliminate the risk of oil spills, the turbines use grease-free hubs and water-lubricated bearings.
In addition to protecting the environment, this ensures easier maintenance and less friction.
The driving force behind innovation is the improvement of material properties:
• Improved resistance to cavitation, corrosion and abrasion.
• Extend equipment life and reduce damage rates.
• Reduced impeller weight and improved mechanical efficiency.
• Improving the workability of materials.
These factors are leading to an increased use of proven and completely new materials, including turbine coatings in wear-resistant stainless steel, fiberglass and high-strength plastics.
Hydrokinetic turbines
Recently, hydrokinetic turbines have become increasingly popular.Unlike conventional water turbines, which require a dam, hydrokinetic turbines use a free flow of water.
Successful prototypes have already been created through intensive research and multi-million dollar investment in tidal energy technology. Most of this subsea equipment is a horizontal shaft hydraulic turbine with fixed or variable blade pitch.
According to industry experts, high-efficiency hydrokinetic turbines will occupy some niches in hydropower over the next decades.
Construction innovation
At present, the average cost of building a hydroelectric power plant can reach 70% of the total project cost.This is a serious reason to look for innovative methods, technologies and materials for construction. For example, the construction of rolled concrete (RCC, rollcrete) dams with a low water content takes significantly less time and requires less investment.
By constructing trapezoidal walls of a cemented sand and gravel (CSG) dam, construction costs can be reduced by about 25%. Another advantage of this technology is that the wide base of the wall provides increased seismic resistance.
Recent improvements in tunneling technology have also reduced costs, especially for small hydropower plants.
Hydropower management improvements
The equipment of the hydroelectric power plant wears out over time and at some point it is irreversibly damaged.This is due to deterioration of the thermal, electrical or mechanical properties of the insulating materials, erosion and corrosion, which leads to fatigue of the turbine steel components.
Clogging of equipment, waterways and sedimentation tanks leads to a gradual decrease in the capacity of the HPP, up to a situation where operating costs exceed revenues. To maintain normal operating conditions, regular maintenance and replacement of damaged and obsolete components are required.
Modernization of hydroelectric power plant could include modifications to reduce environmental impact, such as installing safe water turbines (called fish-friendly turbines) and implementing measures to combat floods or earthquakes in seismically active areas.
Globally, the real productivity of many existing hydropower plants is below their installed capacity. To create the conditions for maximum productivity and high return on investment, companies need to properly manage their assets.
Hydropower asset management aims to effectively maintain or improve performance to the desired level with minimum operating costs throughout the entire life cycle.
If an initial assessment shows that the condition of the assets is unacceptable, investors need to take the most appropriate action to correct the problem. There are 3 options for this, including repair and maintenance, modernization or reconstruction.
When the hydroelectric power plant reaches the age of 30-40 years, a study should be carried out to determine the need for modernization of equipment and components.
Advances in technology have dramatically improved the efficiency of turbines at many existing hydroelectric power plants.
If the flow of water and the existing structure allows it, an increase in the capacity of the hydroelectric power plant could be considered. Several factors determine the need for such improvement, including the current changes in the electricity market.
The use of more and more energy from renewable sources with unstable generation increases the requirements for the management of hydroelectric power plants, especially pumped storage power plants (PSPP).
Replacing equipment (turbine impellers, generator windings, excitation systems, turbine governors, control panels) can provide higher efficiency, reliability and flexibility, as well as lower operating costs.
In general, the potential for increasing the capacity of existing HPPs varies from 10 to 30%. Modernization of turbines is considered economically viable if it leads to an increase in energy conversion efficiency of 4-8% or more.
Most of the world's 45,000 large dams are built for flood control, water storage, agricultural irrigation, fishing or recreation. Only about 25% of these facilities are used for electricity generation. A combination of market change and technical innovation could lead to the expansion of hydropower capacity at some of the existing dams.
HPPs can be built on other existing water structures.
But in most of these cases, the elevation difference is very small, and therefore engineering companies must implement innovative technologies such as hydrokinetic turbines.
Today, there are real technical possibilities for installing hydropower equipment in water supply systems and treatment facilities, which usually have a significant height difference.
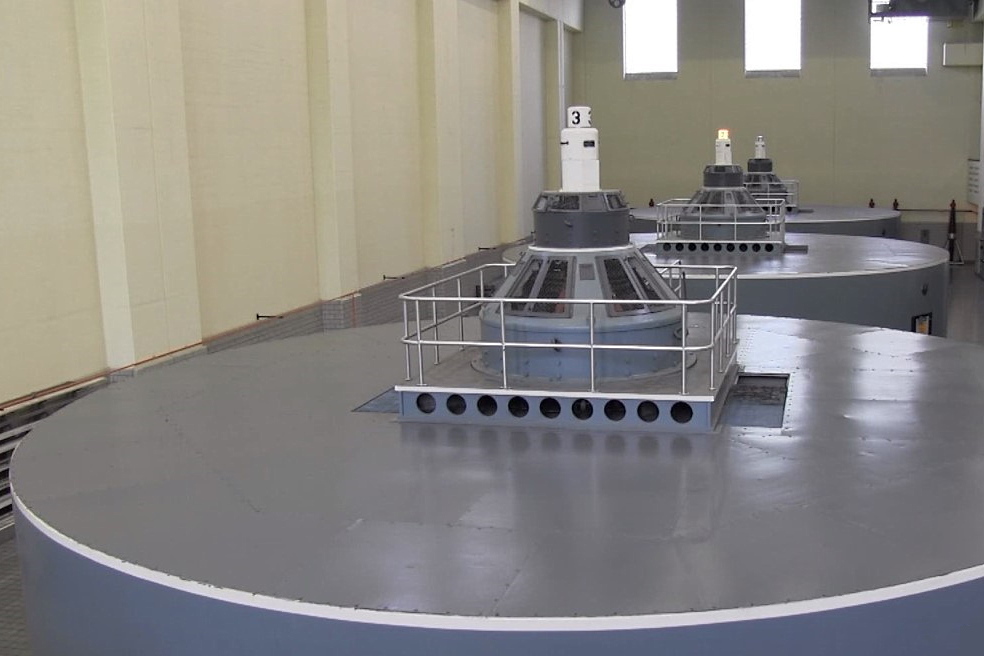
The importance of modernization of hydraulic turbines
Thanks to the development of turbine technology, the modernization of hydropower plants, in addition to adapting them to modern technical standards, has brought real economic benefits in the form of increased electricity production and reduced operating costs.This is partly due to the increased use of double-regulated turbines, which are characterized by high efficiency over a wide range of operating conditions.
The need to standardize equipment for hydroelectric power plants is also mentioned as an important issue. Successful development in this direction can be achieved through the widespread use of computational fluid dynamics, advances in the field of research in hydraulic turbines and the use of standardized solutions.
Preconditions for quality improvement include the reduction in turbine size, the use of modern production technologies and the trend towards factory assembly of turbine equipment.
The modernization of hydraulic turbines includes a set of measures aimed at extending the service life and increasing the efficiency of operation.
The main reasons for its implementation may be the expiration of the service life, breakdown, violation of normal operation or cavitation wear.
Aging of turbines
Practicing engineers know that the service life of hydraulic turbines does not exceed 50 years under normal conditions.After that, the turbine must be modernized to improve its efficiency and prevent emergency situations, which in some cases can have catastrophic consequences.
A prime example is the accident at the Sayano-Shushenskaya hydroelectric power plant in 2009, which resulted in casualties, multi-million dollar losses and significant environmental impacts. In principle, signs of wear on any hydraulic turbine element is a reason for modernization.
Cavitation wear of hydraulic turbines
It is known that modern hydraulic turbines are designed to operate in the initial phase of the development of cavitation processes in the flow path.Sometimes hydraulic turbines are operated outside the conditions set by the manufacturer, which leads to accelerated cavitation erosion of the metal. This reduces, sometimes quite significantly, the normal life of the turbines, and the need for modernization of the flow path becomes obvious.
General approach to the modernization of hydraulic turbines
Regardless of the type and parameters of the turbine, the modernization process most often goes through the following stages:1. Analysis of the turbine condition, which includes the following:
• Study of the available technical documentation.
• Measurements of the dimensions of the flow path of the turbine.
• Detailed analysis of reports on equipment operation.
• Analysis of the possibilities of increasing the turbine power.
• Establishing the actual values of external dimensions.
• Experimental determination of turbine characteristics.
2. Preparation of a detailed report analyzing the technical and economic aspects of modernization.
Preparation of a proposal for the required scope of work (the decision is made by the owner).
3. Calculation, design and manufacture of the necessary turbine elements. If necessary, engineers perform tests to refine the parameters.
4. Assembly of elements and installation of a hydraulic turbine.
5. Start-up and experimental determination of the characteristics of the modernized turbine. Monitoring of work under load.
Common modernization challenges
When modernizing hydraulic turbines, the following problems most often arise:• Limitations (especially in old designs) of the geometric compatibility of new elements with existing parts of the turbine.
• Ensuring that the kinematic parameters of the flow at the inlet to the impeller match those at the outlet (for jet turbines).
• Limited ability to change the diameter ratio for Pelton turbines.
• Extremely limited possibilities of reducing the clearances between the impeller and the working chamber without upgrading the turbine bearings.
Advantages of periodic modernization of hydraulic turbines
Following the modernization of hydroelectric power plants, the customer can expect a significant increase in electricity production and improved operational reliability.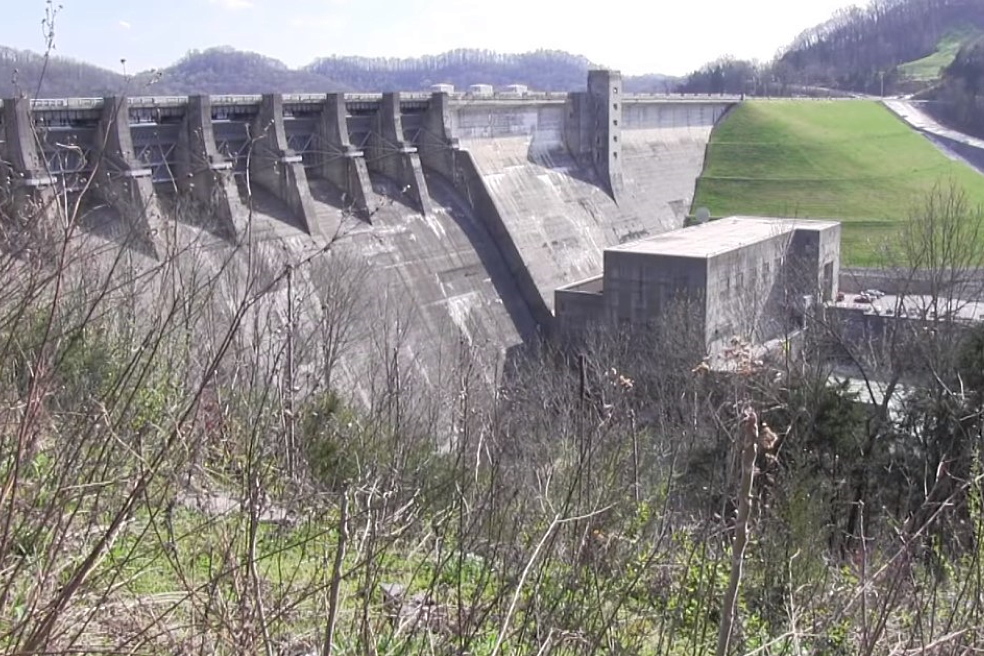
The advantages of modernizing a hydraulic turbine are as follows:
• Improving the efficiency of the workflow.
• More efficient control of the turbine and hydraulic unit.
• Increased cavitation resistance of the hydraulic turbine flow path (the result of modern calculation methods, as well as new materials).
• Significant reduction in the operating costs of the hydropower plant.
• Reducing the gaps between the impeller and the working chamber in Kaplan turbines, in addition to reducing losses, leads to a decrease in the risk to fish.
• Modern technologies minimize the likelihood of water pollution by oils and toxic substances (Kaplan turbines and diagonal turbines).
• Improving the reliability of the turbine and hydraulic unit.
• More efficient water aeration.
The technical condition of the rotor, bearings and seals is essential for the correct operation of the hydraulic units.
Years of field experience have shown that damage to these components is the most common cause of reduced HPP efficiency and availability.
For this reason, the modernization of individual parts of hydroelectric power plants should be carried out with simultaneous diagnostics and repair work affecting all the main components and assemblies.
Construction and modernization of hydroelectric power plants under the EPC contract
The role of EPC contracts in the energy sector is growing every year.This is due to the obvious advantages of this type of customer-contractor relationship in the context of complex projects with many stakeholders.
EPC refers to a form of project management and associated engineering design process that is prevalent in international engineering and especially in the hydropower sector.
This includes a complete engineering service, procurement and manufacture of all materials and parts, assembly on site, testing and commissioning.
According to the EPC contract, the necessary permits (with the exception of those that the customer is obliged to obtain by law) are obtained by the general contractor. Administrative costs for the client are minimal with this approach.
The advantage for the customer is that he does not need to allocate significant human and material resources to constantly monitor work, conclude contracts with small subcontractors and overcome bureaucratic barriers. To implement a project, the customer requires a relatively small number of employees.
The cost of modernization of hydroelectric power plants under an EPC contract may be slightly higher, but this “simplified” approach has clear benefits for smaller customers.
Costex Corporation DBA also offers financing and lending for the modernization of hydroelectric power plants.
To find out more, contact us at any time.