To consider an application for financing, fill out the form and send it to us by e-mail along with the project brief, or contact our experts
Along with the development of the energy sector, mechanical engineering, metallurgy, electronics and the chemical industry, the construction of modern cement plants largely determines the industrial potential of the country.
Cement plants are one of the most energy-intensive and material-intensive industries, which also emit huge amounts of harmful dust, gases and waste water.
Some researchers believe that the production of building materials consumes about 50% of the total amount of energy produced by mankind and up to 60% of all raw materials used in industry.
This fact, along with high investment costs and strict environmental requirements, requires close attention and a professional approach to investment planning, engineering design and construction of cement plants.
The cement industry now forms the backbone of the modern construction industry, supplying the basic material for the production of building structures and parts. The leading consumers of cement are manufacturers of various types of reinforced concrete products that carry out capital construction. Cement, which is essentially a finely divided powdery mixture of inorganic binders, has become an increasingly complex high-tech product in recent decades, produced in hundreds of different variations.
The growing technical complexity and variety of cement products inevitably affects the investment costs associated with the construction and modernization of production facilities.
The cost of building medium-sized factories is currently estimated at between 150 and 300 million euros, which is a significant investment even for companies in good financial health. This requires the development of a detailed financial plan to attract large borrowed funds, usually in the form of bank loans.
Costex Corporation DBA, an international company headquartered in Spain, offers project financing and long-term lending for the construction of cement plants.
If you are planning the construction or modernization of a cement plant, please contact our representatives at any time, our partners will also help resolve this issue.
Cement plant construction stages
The key to successful investment planning and attracting external funding is a clear project schedule that should take into account potential risks and leave room for adjustments to meet the interests of all project participants.In most cases, it is assumed that the cement plant project will be implemented within 2-3 years, from the development of the project to the launch of the first production line. Some project stages may overlap, as different areas of work are carried out in parallel to speed up the commissioning of the facility.
The approximate construction schedule for the cement plant is shown in the table below.
Stage | Content | Terms of work |
Site preparation | At the initial stage, construction teams manually and mechanically clear the construction site from vegetation, level the soil and fill the territory of the future plant with limestone or other available materials. At this stage, temporary access roads are being built, special areas for parking special vehicles and storage of materials are being set up. | 4-8 months |
Civil works | The stage of general construction work includes pouring the foundations of buildings and erecting the frames of all structures for placing equipment. At this stage, a limestone quarry is also being built and the site is being prepared for the installation of conveyor belts and crushing equipment. Facilities for storing mineral raw materials are also being prepared. Silos, bunkers for clinker, supports and buildings for a clinker kiln and chiller, fuel depots, a hazardous waste warehouse, workshops, administrative buildings are being erected. | 12-18 months |
Installation of equipment | The installation phase overlaps with general construction works. To shorten the overall plant construction time, several construction teams install clinker kilns, mills and other equipment as soon as the appropriate supports and foundations are erected on site. At this stage, underground communications are being built and sewage treatment facilities are being equipped. Power transmission line supports are installed and communications are supplied. If necessary, water storage tanks are also installed. | 8-12 months |
Finishing work | The final stage of the construction of the cement plant is finishing work, which includes finishing of internal surfaces, installation of heating and air conditioning equipment, plumbing equipment, non-slip floors, demarcation equipment, etc. | 3-6 months |
Given the enormous volume of administrative, engineering, construction and financial tasks, an increasing number of companies around the world are opting for comprehensive general contracting services.
The EPC contract offers customers a number of important advantages in the context of the construction and operation of technically complex facilities.
Advantages of construction under an EPC contract
EPC contracts, also known as turnkey contracts, are one of the most advanced forms of project management.This abbreviation stands for Engineering, Procurement and Construction, and in this contractual model, all risks associated with the work fall on a single general contractor.
By signing an EPC contract for the construction of a cement plant, the company initiating the project transfers full responsibility for the project to a specialized engineering company, implying the timely and high-quality implementation of a range of services for engineering design, procurement of equipment and construction.
The benefit to the client is that the contractor sets a fixed price that will not change, even if the work requires additional costs not foreseen in the original contract. Also, the client does not need to allocate human resources to control the project, instead, it is enough to just wait for the actual launch of the plant in operation and the transfer of the facility.
Moreover, in some cases, the contract provides for the launch and professional operation of the cement plant by qualified specialists before it reaches its planned capacity.
The contractor's team is also responsible for the development of the limestone quarry and the implementation of other works necessary for the successful operation of the facility.
The second advantage of an EPC contract is that the client knows exactly when the finished facility will be commissioned. Thus, the contractor is responsible and obliged to compensate the client for financial losses in the event of a delay in work. This allows stakeholders to accurately coordinate financial flows associated with high-value construction.
Finally, specialized engineering companies provide the customer with professional experience, highly qualified personnel, advanced equipment and technologies for the correct development of the project and solving potential problems during its implementation.
While in general EPC contracts seem to be favorable to customers, this choice is associated with some increase in investment costs, ranging from 10 to 30%.
Due to the high costs, this option is most relevant for large projects, where professional services provide a critical advantage.
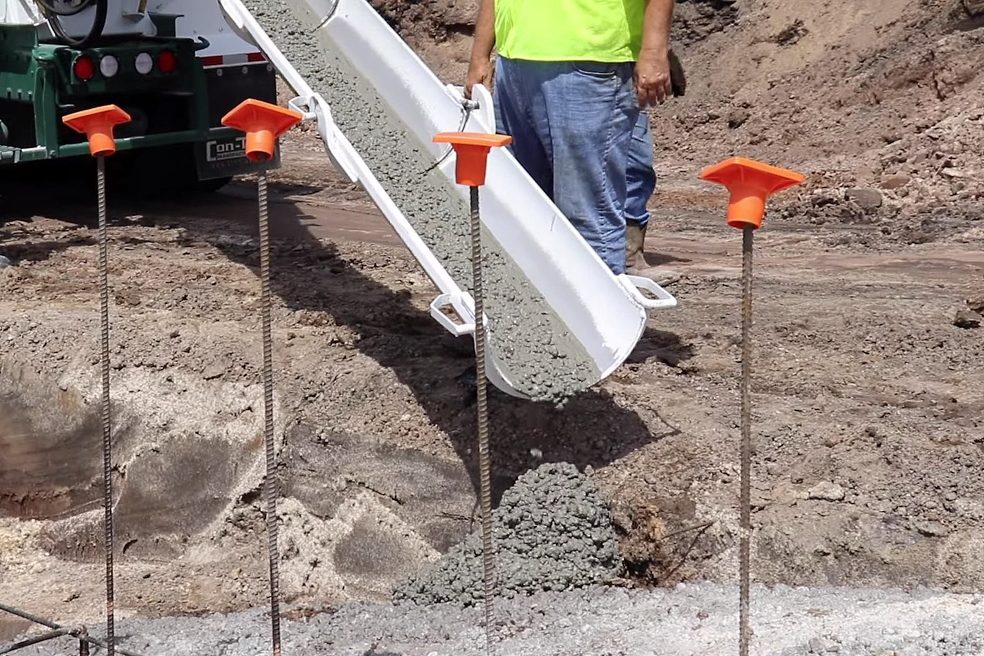
General information about cement production
Cement, which is complex and diverse in its chemical composition, is produced through a series of energy-intensive and costly technological processes.Typically, cement plants are built in close proximity to raw material extraction sites, which helps to minimize transportation costs.
Cement production includes the following stages:
• Extraction of raw materials and their delivery to the plant.
• Crushing and grinding of raw materials to the required degree.
• Mixing of components, preparation of a raw mixture.
• Firing the resulting mixture for the production of cement clinker.
• Grinding of clinker with additives to obtain cement.
• Packaging and labeling of finished products.
Thus, the production of finished cement can be divided into two broad stages.
The first is the production of clinker.
Secondly, this is bringing the clinker to the required powdery state with the simultaneous addition of gypsum and other processing aids in accordance with a specific recipe.
The practice of cement production, that the first part is the most energy-intensive and expensive, accounting for 60-70% of the cost of finished cement. This includes the costs of extracting and transporting mineral raw materials, grinding, drying and burning the mass in a clinker kiln at high temperatures with the combustion of fossil fuels (natural gas).
Cement plant construction requires a rational approach to engineering design, planning, placement and connection of equipment, including crushers and grinders, conveyor belts, cement silos, coarse mills, dryers, cement separators, coolers, kilns, special equipment for packaging and transportation of finished products.
The construction of any cement plant begins with the development of quarries for the extraction of mineral raw materials, which should be located as close as possible to the production site to minimize costs. The development of limestone deposits requires significant costs, since natural limestone deposits are usually located at a depth of 10-15 meters, extending in a thin layer over a large area.
The resulting limestone is transported by conveyor belts to the grinding equipment, where large pieces of the mineral are turned into small particles and mixed with other components for further processing.
An important step is the drying of the raw materials and the burning, which is carried out in special rotary kilns and requires a huge amount of energy.
The construction of a rotary clinker kiln requires a lot of space, since these horizontally oriented structures often exceed 200 meters in length.
The second stage of the production process includes crushing clinker, drying mineral additives, crushing limestone, followed by grinding together with the corresponding mineral components of the cement mixture. The choice of specific equipment and technological chains for this stage is made by the engineering team, taking into account the type of product, the quality of raw materials, requirements for the quality composition of the finished product and other factors.
Since the sources of raw materials differ significantly from each other, the specific approach to the construction of a cement plant should be unique in each case.
The chemical composition of the cement raw material, the strength and initial moisture content of the particles, and the applicable environmental requirements influence the choice of production method.
Choice of cement production method
Depending on the method of preparing cement raw materials for firing, engineers distinguish several methods of cement production, including wet process, semi-dry process, as well as dry and combined production of cement clinker.The choice of methods for the production of cement clinker is determined not only by technical and economic considerations, but also by the characteristics of the raw materials.
When the moisture content of raw materials is more than 10%, engineers consider a wet process to be more expedient.
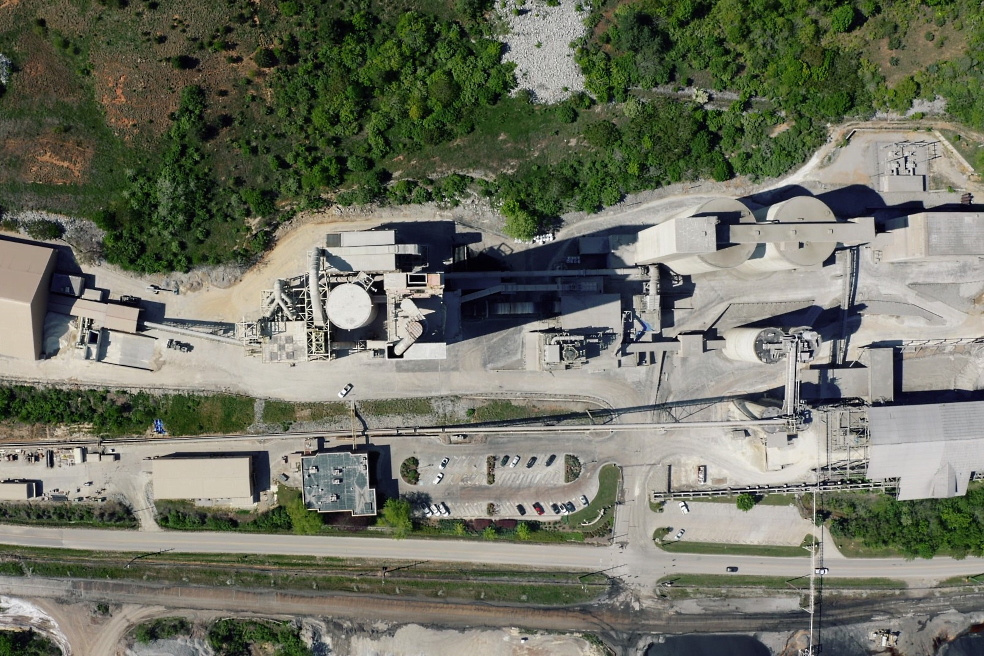
Each method has its own advantages and disadvantages, which the engineering team weighs and takes into account when designing and building a cement plant.
For example, water makes it easier to grind most materials and helps to achieve a homogeneous mixture, but increases the energy consumption for clinker firing by up to 40%.
The wet method of cement production requires the construction of clinker kilns of a larger volume, since a significant part of them performs the function of a water evaporator during firing. This affects the layout of the future plant and the location of its individual zones.
This process is beneficial to use when organizing the production of cement using several soft components, such as clay, which are easily ground in the presence of water. In the case of production of cement clinker from homogeneous solid raw materials with low moisture content, the dry method is considered appropriate. Semi-dry method of cement production is recommended for plastic raw materials, which, when granulated, form heat-resistant and mechanically strong granules.
The material obtained as a result of processing the mineral mixture in a wet process has the form of an aqueous suspension with a water content of up to 50%.
This material is delivered to special rotary kilns, where it is fired and turned into large granules, which are subjected to thorough grinding at the final stage.
The dry production process is characterized by drying the mixture just before grinding. Thus, the resulting mixture is in the form of a finely divided and dried powder. In general, this method is considered to be more economical.
The essence of the combined process is that the cement mixture is produced by the wet method, and then partially dehydrated and fired in a clinker kiln in the form of a semi-dry mass. The combined method has several varieties, each of which requires a special technological chain and equipment.
There is also a clinker-free method for the production of cement, in which raw materials (for example, blast furnace slag) are combined with other substances and converted into a special slag mixture.
This mixture is then finely ground on grinding equipment to the desired state, turning into ready-made cement.
The last method has the advantage of minimizing the consumption of electricity and fossil fuels.
Clinker-free production of cement from slag can be an ideal option for organizing a waste-free production cycle due to the use of waste from metallurgical enterprises.
If you need financing or are interested in the construction of a cement plant, please contact LBFL at any time.