Financing, construction and modernization of sea container terminals
Costex Corporation DBA offers:
• Investment financing from $ /€ 5 million or equivalent and more
• Minimizing the contribution of the project promoter
• Investment loan term up to 20 years
• Credit guarantees
The share of containers in the maritime transport market is also growing steadily.
Container terminals are an essential element of the future global intermodal transport system.
Modern seaports act as key hubs for international trade, and international agencies are increasingly focusing on the financing and construction of marine container terminals, especially in terms of efficiency, innovation and expansion of the global network.
Currently, the largest container terminals are located in East Asia, mainly in China. However, companies around the world are interested in the construction, modernization and expansion of these facilities. For this reason, LBFL engineering services are in great demand in the Middle East, Europe, USA, North Africa, Latin America and other regions of the world.
Since its inception, containerization has remained one of the most important ways to consolidate and transport cargo.
Containerization helps to pack a consignment into a separate compact unit while maintaining shape, size and weight during transportation, handling and storage, that is, during the entire transport cycle.
Today, container terminal operators have to take into account the rationalization and reorganization taking place in different parts of the transport chain and having a direct impact on their activities. Engineering design of a container terminal every time becomes a serious challenge for contractors, requiring an innovative and individual approach to the project.
The goal of our engineering team remains unchanged.
We strive to increase the efficiency of loading and unloading operations, ensuring the reliability and stability of terminals without excessive financial costs.
This requires not only the use of TOS, large automated gantry cranes and AGVs, but also the introduction of innovative logistics models.
LBFL is also ready to offer you long-term project financing for the construction of seaports and container terminals on favorable terms with the involvement of large private investors, venture funds and leading European banks.
Improving the operation of container terminals: engineering and construction
Transhipment operations require planning skills and in-depth knowledge, the goal of which is to provide the right container of the required volume at the right time to meet the needs of shippers.For the terminal operator, this means a constant change in the location of containers, which is the result of an imbalance between cargo flows. Engineering design of marine container terminals requires an understanding of the specifics of the work and needs of operators, as well as close contact with the customer at all stages of the process.
A container terminal operates in a similar way to a manufacturing plant that receives “raw material” and turns it into a “finished product”.
Any operations carried out with containers give them a higher added value, even though the cargo is not physically transformed.
These operations include, for example, loading and unloading containers onto / from vehicles, and sometimes loading or unloading cargo from containers. Ultimately, the loaded containers leave the terminal as a “finished product”.
By minimizing the time spent by containers in the port, the terminal can increase the number of containers handled and thus increase its throughput. The entire process of unloading and loading is aimed at reducing the time spent by the ship in the port, as well as ensuring the stability of the ship.
Optimal unloading of containers involves temporary stacking of containers in rows, requiring heavy cranes of appropriate height and configuration. The advantage of stacking is that the containers take up less storage space, and the disadvantage of this system is the complexity of handling the containers, which requires special organization of the terminal.
The yard of the container terminal consists of a whole complex of buildings for administrative activities and places for stacking containers, roads for container transportation, various handling equipment, etc.
The specific structure of the storage yard depends on the space available, and if the port has rail links, the container terminal must also be equipped with rail tracks and platforms.
Loading and unloading equipment
Considering the huge variety of unpredictable factors affecting the efficient operation of a container terminal, experts believe that there is no “ideal” model. Each new project requires a customized approach to solving certain problems.The main handling equipment for the marine terminal includes:
• STS, Ship-to-Shore Gantry cranes.
• RTG, Rubber-Tyred Gantry cranes.
• RMG, Rail-Mounted Gantry cranes.
• TTU, Tractor-Trailer Units.
• AGV, Automated Guided Vehicles.
• ECH, Empty Container Handlers.
• SC, Straddle Carriers.
• RS, Reachstackers.
The equipment listed above is used at various scales and in numerous combinations.
In particular, when using a reachstacker in conjunction with TTUs, a multi-ton gantry crane places containers on tractors that transport them to storage locations.
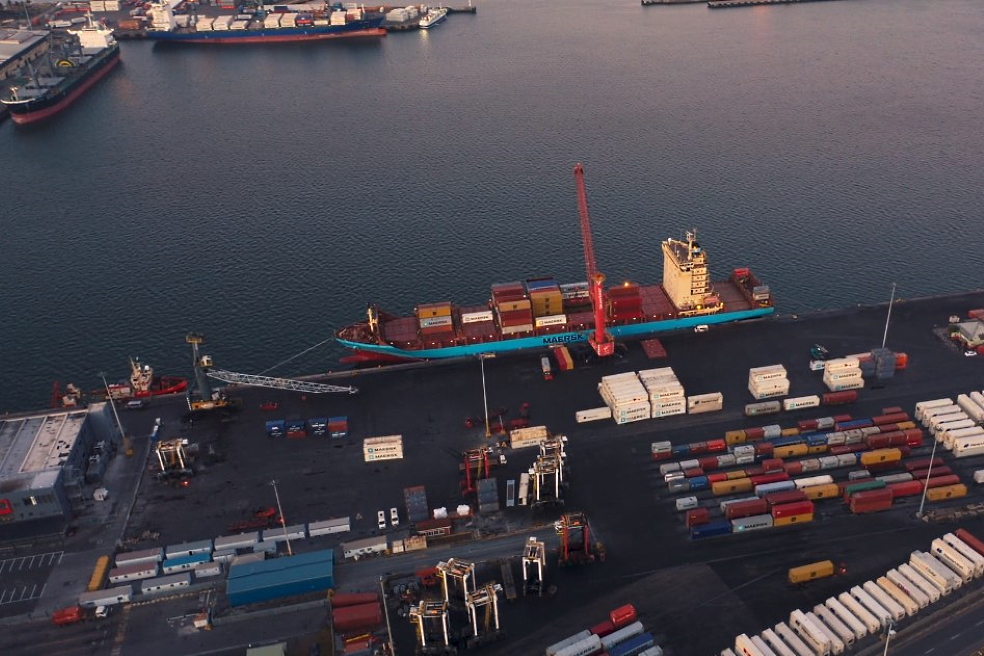
In storage areas, containers are distributed using appropriate devices (container spreaders) that easily lift heavy loads, operating at high speed and operational efficiency.
Use of reachstackers and terminal tractors
Traditionally, heavy straddle carriers have been used for this operation, but reachstackers are now used by most container terminal operators due to the greater operational capability and stacking density.Due to its versatility, the reachstacker is often the best choice for small to medium sized container terminals or multifunction terminals. It is easy to operate and is especially widely used in countries with a shortage of trained personnel.
The main advantages of the system are low capital investments and ease of organizing the process. Reachstackers and terminal tractors have a relatively low investment cost per piece of equipment.
Their operating costs are also relatively low compared to other alternative systems.
On the other hand, the disadvantages of this system are high personnel requirements due to the large number of vehicles and low levels of automation, so operating costs may be higher in countries with high labor costs.
Tractor-trailed units cannot independently raise or put down the container, and during the simultaneous loading and unloading of tractors on a cramped site, the work is disrupted. It is important to consider the way of work at the stage of engineering design and construction of a container terminal, choosing the best solutions.
Using straddle carriers
Large container terminals often use straddle carriers (SC).This system is flexible and fast.
Ship-to-shore gantry cranes deliver containers to the dock, from where they are transported to the site.
Straddle carriers are independent of other devices and can perform all container operations. In some terminals, the system is supported by empty container handler and RMG cranes for loading railcars.
Containers can be temporarily stored on the ground with short waiting times for handling equipment. This allows the cranes to achieve high productivity, so that a large number of simultaneous movements of containers can be observed in such a container terminal.
Failure of one SC has relatively little effect on the overall process.
Compared to systems using TTUs, labor costs are lower due to the much smaller number of vehicles used.
The disadvantages of this system are the high investment costs for the construction of handling equipment and the subsequent costs for its maintenance, mainly electricity. Labor costs are also relatively high compared to semi-automatic transport and storage systems.
The storage area should be built more spacious due to the low stack height and provide higher traffic.
For long-distance transportation, straddle carriers are not considered the best choice. Compared to tractors, they are slow and, most importantly, expensive.
Using gantry cranes
Large terminal operators often choose a system based on rubber-tyred gantry cranes (RTG).This system requires the construction of wide storage areas with strict security measures.
Ship-to-shore gantry cranes load containers on tractors that transport the cargo to a storage yard where an RTG crane stacks them. These cranes provide a very high stacking density due to their significant lifting capacity.
Taking into account the operations associated with the external movement of cargo, one STS crane usually requires 2-3 RTG cranes and 4-5 terminal tractors. RTG cranes stack containers in stacks 2–4 tiers high, up to 8 containers wide, leaving gaps between the stacks for reloading.
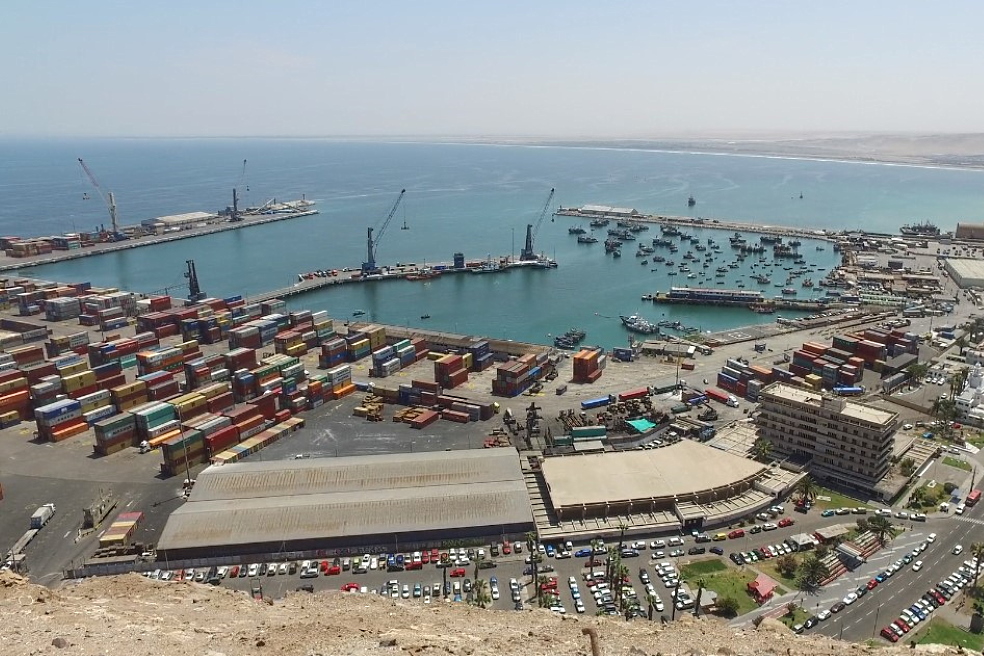
Using such a system, a container terminal can store about 1000 TEU per hectare. This figure is very important. The engineering team, based on the method of loading and unloading operations and the planned cargo turnover, must design optimal storage areas, platforms, driveways and other elements of the facility.
The terminal, based on the use of rail-mounted gantry (RMG) cranes, includes two subsystems – terminal tractors and automated guided vehicles (AGV), controlled by the operating system.
The first subsystem, which includes terminal tractors, performs the same tasks as the system with RTG cranes. Its distinctive feature is that gantry cranes are installed on permanent railway tracks, and containers are stored in higher and wider stacks.
Thanks to the described system, the container terminal can store more than 1000 TEU per hectare. This engineering solution is very reliable and also affordable in terms of initial investment and moderate equipment maintenance costs.
The RMG system is also susceptible to automation.
Use of automated guided vehicles
One of the most efficient solutions for marine container terminals is the joint use of an RMG crane and automated guided vehicles (AGV), designed mainly for horizontal container transport.For the safety of such terminals, automation should be implemented only in the area where AGVs operate and the area where the equipment is served by the terminal staff.
AGVs accept containers at the ends of stacks, and container handling is mainly done with automatic rail-mounted gantry cranes. The obvious advantages of such an organization of work are very low labor costs and ample opportunities for equipment automation.
This engineering solution is very efficient due to the high speed of horizontal movement of containers across the warehouse area.
The disadvantages of the system are high investment costs as well as the need for well trained staff.
Also, container terminals of this type are difficult to modernize, which makes it almost impossible and impractical to make subsequent changes.
Regardless of the type of your terminal, LBFL's engineering team is ready to select the optimal logistics and technical solutions, adapted to the needs of a specific project. Contact us to find out more.
Automation and modernization of marine container terminals
The degree of automation of container handling is a determining factor in the development of modern seaports.This indicator is important for achieving high efficiency in international trade.
The modernization of container terminals is aimed at the following:
• Reducing the time of unloading and loading the ship with container cranes.
• Improving the efficiency of road and rail transport, which is responsible for the movement of goods within the port and their shipment to customers.
• Increase in labor productivity of container terminal employees, determined by the number of containers handled per employee.
• Gradual reduction of energy consumption by 1 TEU.
To achieve these goals, the company LBFL offers a wide range of engineering solutions.
First, the terminal must be equipped with cranes that can efficiently handle ships of all sizes.
Secondly, modern container terminals are equipped with reliable automated systems that carry out fast and accurate loading and unloading operations with minimal human intervention.
Finally, we and our partners offer operators the latest automated equipment to integrate all cargo handling processes.
TOS (Terminal Operating System) play a key role in increasing the competitiveness of container terminals.
These are universal IT systems that ensure the continuity, high speed and safety of container handling.
Innovative integrated control systems ensure fast reloading, and modern sensors ensure greater accuracy in any transport task, eliminating equipment downtime. The main advantage of TOS is the fast flow of information, which allows control center operators to support the decision-making process for maintaining the technical condition of port facilities and monitoring logistics processes.
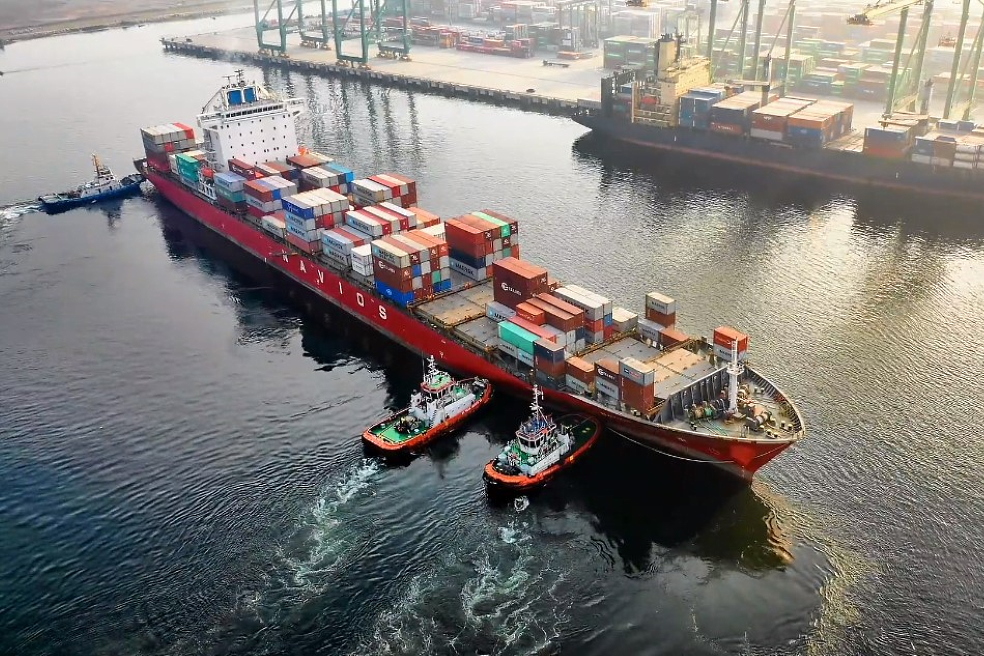
Thanks to advanced solutions in the field of automation, the process of unloading a ship is fundamentally different from what it was known 20-25 years ago.
Automated loading and unloading operations are as follows:
• The operator in the crane cab uses computer systems to locate the container on the ship, pick it up, and then the container is automatically sent to the delivery line, where it is loaded into an AGV (Automated Guided Vehicle).
• AGV delivers the container to the site for an automatic crane, which places the container at a predetermined location.
• The whole operation is controlled by the advanced terminal operating system TOS, which eliminates accidental errors and streamlines the process.
• Containers stored in stacks are loaded onto tractors in a semi-automatic mode, or they are automatically sent to AGV, which transports them to the railway platform.
In major European seaports such as Rotterdam, container terminal automation started earlier than others.
This practice has been shown to be highly effective, resulting in increased loading and unloading speeds while reducing the number of dock workers. The modernization of container terminals around the world is moving towards universal automation and computerization.
For example, in 2017, the Qingdao port was the first in Asia to acquire an automated container terminal QQCTN, which significantly increased the port's handling capacity and provided multi-million dollar savings.
The experience of operating such systems shows that the need for personnel can be reduced by 70% or more while increasing the speed and safety.
Moreover, a computerized container positioning system and a scanning laser ensure that the container terminal operates smoothly in the dark.
Our services for large businesses
In recent years, many container terminals have faced serious problems, primarily due to fierce competition from new players, in particular, cargo carriers, logistics companies and investment groups.The ever-changing economic environment means that terminal operators are becoming more cautious about their future prospects. Despite the expected growth in the future, companies are much more careful in choosing new locations for new investment projects.
State-of-the-art engineering solutions, coupled with flexible sources of project finance, drive industry growth and enhance the competitiveness of individual companies.
International company LBFL offers the following services:
• Financing the construction of container terminals.
• Engineering design, purchase and delivery of special equipment.
• Construction of marine container terminals under the EPC contract.
• Modernization and expansion of existing facilities.
• Implementation of automation systems.
Our team implements large infrastructure projects around the world, using the most advanced technical solutions and financial schemes for our clients.
Contact us at any time to discuss the details of your project.